鍛件資訊
2021-03-15 16:27
石化用特大型管板鍛件系我公司重點鍛件研發方向之一。近幾年來,通過不斷加大技術研發力度,持續提升管板鍛造技術實力,在管板鍛造方面,我們取得了長足的進步。我公司負責生產的∮8000mm 特大型管板鍛件是建廠以來的最大鍛件。合格等級為:單個缺陷2級,底波降低量1級,密集型缺陷1級。晶粒度要求不低于6級,嚴格控制非金屬夾雜物含量。在生產、技術等方面都遇到了極大挑戰。為解決這些難題,通過不斷創新、探索,合理設計鍛件圖,提出新的鍛造變形工藝,最終完成了管板鍛件的生產試制,提升了公司特大型管板鍛件的制造能力。
1 鍛件工藝圖設計
1 鍛件工藝圖設計
∮8000mm特大型管板鍛件直徑大,重量重,采用整體成形難度極大,只能采取分段成形。以前,對于規格相對較大的管板鍛件通常鍛成方板,然后拼焊成形。顯然,若采用該種成形方法,鍛件重量大、成本高,因此必須提出一種新的鍛件工藝圖:既能保證鍛件內部空洞疏松等缺陷得到壓實焊合,又能降低鍛件成本,滿足客戶鍛件減重的要求。
基于此,我們優化了鍛件工藝圖并充分利用金屬流動規律,提出了分三段成形,即:中間長弧板成形+兩端半弧板成形,鍛件形狀最大限度的接近零件形狀的工藝設計方法,極大的減輕了鍛件工藝重量,降低了鍛件制造成本。
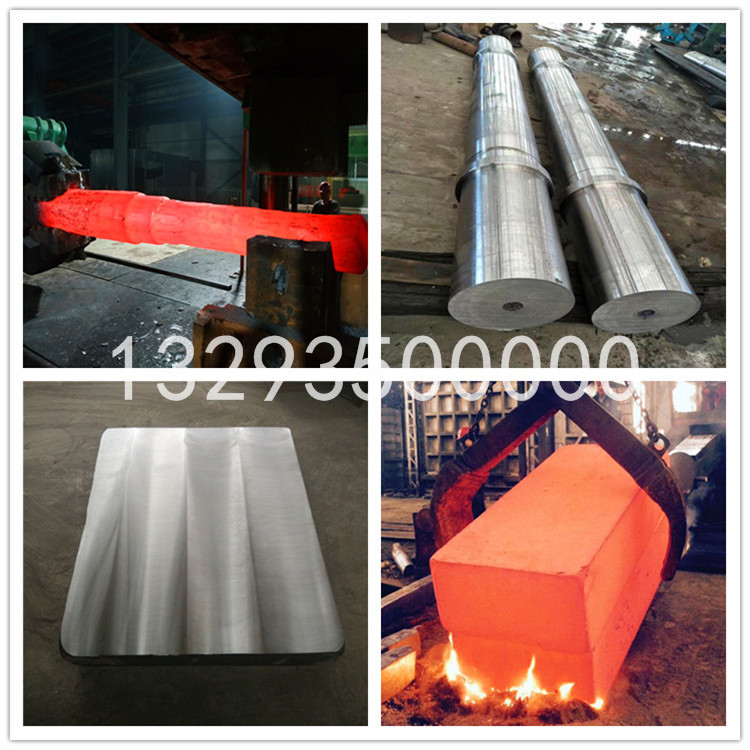
2.1兩端半弧板成形工藝研究
半弧板鍛件形狀較復雜,按照傳統工藝方法損料多,材料實際利用率相對較低,必然增加車間生產成本。通過認真分析鍛件形狀,確定采取兩件錯位合鍛-氣割成形的方法組織生產。
通過采用兩件合鍛的成形工藝,不僅降低了鍛件工藝重量和工藝損耗,而且克服了因鍛件形狀復雜導致車間組織生產難度較大的問題。
2.2中間長弧板成形工藝研究
長弧板鍛件形狀較特別,若按照傳統工藝方法直接鍛成方板,則增加了鍛件工藝重量。通過認真分析鍛造變形工藝,基于金屬塑性流動原理,通過充分利用鍛造過程中產生舌頭鼓出兩端弧形,不僅容易保證鍛件兩端的弧度尺寸,而且生產操作控制簡單,也降低了鍛件制造成本。
2.3主變形方案分析
由于本批次管板技術要求嚴格,而且截面大、高度低,心部極易產生片狀夾雜缺陷,基于此主變形鐓拔階段采取寬砧強壓拔方法,大進砧量、大壓下量進行鍛造,充分打碎粗大組織,焊合孔洞性缺陷。W/H(W一砧子寬度,H一坯料壓前高度)控制在0.5-0.8,保證坯料心部的應力、應變狀態。壓下率△H/H控制在16%~22%,保證閉合面積最大。主變形拔扁初始階段采取寬砧強壓拔扁、坯料局部成形,金屬基體以局部整體流動為主,使得受壓部位心部承受一定的靜水壓力,減弱了夾雜物成為片狀的趨勢。拔完一趟后翻轉180°進行第二趟拔扁,壓下率△H/H 控制在 14%~17%之間,合理控制送進量。主變形拔扁接近出成品階段采用窄砧拔扁拔長。變形進行到此階段,內部組織基本上得到了充分壓實,成形力較大,金屬流動較為困難。采用窄砧拔扁拔長降低了成形力,再則砧子與坯料的接觸面積減小,一定程度上改善了金屬塑性流動狀況,利于鍛件成形。
2.4 工藝方案主要亮點和過程控制關鍵點
(1)該工藝方案主要亮點:很大程度上實現了按照管板零件輪廓形狀進行成形,且生產操作較為方便,尺寸也較容易控制。兩端半弧板鍛件錯位合鍛-氣割的工藝方法一定程度上解決了形狀較為復雜大型鍛件的成形問題,且通過合理利用兩端余料鍛制本體試板,更好的貼合了鍛件本身綜合性能。長弧板的鍛造充分利用了金屬流動規律,解決了端部弧形輪廓的成形,達到了降低生產成本的目的。
(2)該工藝方案生產過程控制關鍵點:鐓拔階段嚴格按照工藝參數進行生產操作,合理控制進砧量和壓下量。拔扁過程中應根據具體生產情況及時調整操作方法,保證鍛件成形質量。另外,由于鍛件形狀的特殊性,接近工藝尺寸后,要及時用事先做好的樣板比對,特別要關注長弧板兩端弧度的成形情況,防止尺寸超差。
3 生產試制
結合以上分析、研究,采用該成形工藝進行了生產試制。
在試制中,嚴格按照工藝參數組織生產,合理控制進砧量和壓下量,最終成功完成了兩件特大型管板(四件半弧板、兩件長弧板)的生產,經后續超聲檢測、晶粒度和非金屬夾雜物檢驗,全部滿足交貨要求。
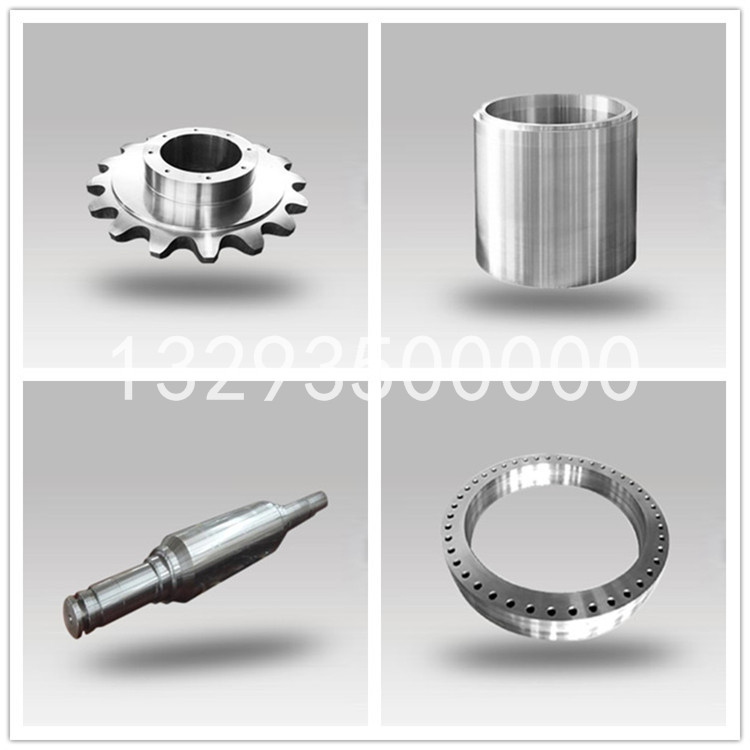
經分析和生產試制,可以得到以下結論:
(1)對于特大型管板鍛件采取兩端半弧板、中間長弧板的成形新工藝方案是切實可行的,也滿足了客戶降本增效的要求。
(2)采取寬砧強壓拔方法鍛制管板能夠有效焊合內部缺陷,避免片狀夾雜缺陷超標,保證了鍛件內部質量。
(3)該工藝方案生產操作較為方便,尺寸容易控制,豐富了特大型管板鍛件的成形方法,為后續不同類型、規格的鍛件生產提供了技術支撐。